Case Study | Taking care of your treatment plant
Once we have a treatment plant installed, it is easy to put it out of our minds and expect everything to function perfectly. Well, at ASL, we want that to be the case for all our customers and for that reason, we come back and check on the treatment plants that we install. We do this A to check that all is mechanically running smoothly and B to see how the household usage affects the functionality of the treatment plant.
Unfortunately, it is easy to underestimate how detrimental the effects of fat, oil and grease can be to the mechanics and, in turn, successful function. We try to point this out to all our customers, but it is a present and real issue for ALL drainage systems, whether private or public.
The following is a case study based around a historic job that ASL carried out, but the dates and any identifying details have been changed or removed for privacy reasons.
Observations & Findings
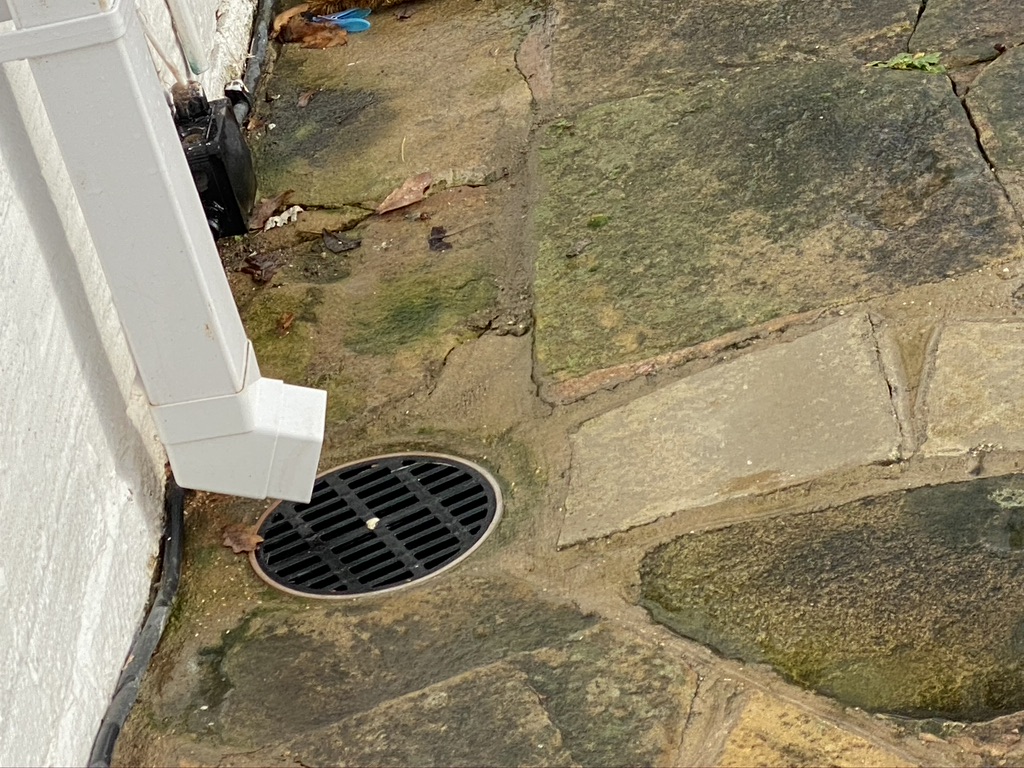
RE: Attendance to estimate drainage works reference surface water and roof water entering sewage pipes & inspection chambers leading to the treatment plant.
We attended the property with our pre-loaded lorry holding approximately 4000 litres of clean water and various equipment to carry out several tests to the drains to establish the infiltration of surface water entering the sewage system.
Please see our findings as follows:-
Steel-plated covered inspection chamber.
- During the test, surface water poured towards the steel plate. Bearing in mind the top 400mm of ground is non-porous.
- The steel plate covering the chamber is ill-fitted, with large gaps all around the opening. This is open to the elements beneath the edge of the footpath. Surface water can enter the chamber from under the footpath, as well as under the steel plate.
- The base for the brickwork is called benching; inspection today, as revealed, surface water is leaking between the brickwork and the benching.
- As you are aware, the channel in the chamber is continually running with clean water, later confirmed to be surface water. At approximately 2m upstream of the chamber, we discovered an open joint, shown to you, a pipe that allows a great deal of groundwater to enter the pipe (we took a recording of this).
- The pipe from the steel-plated chamber runs upstream, beneath the property, to the inspection chamber on the opposite side of the building.
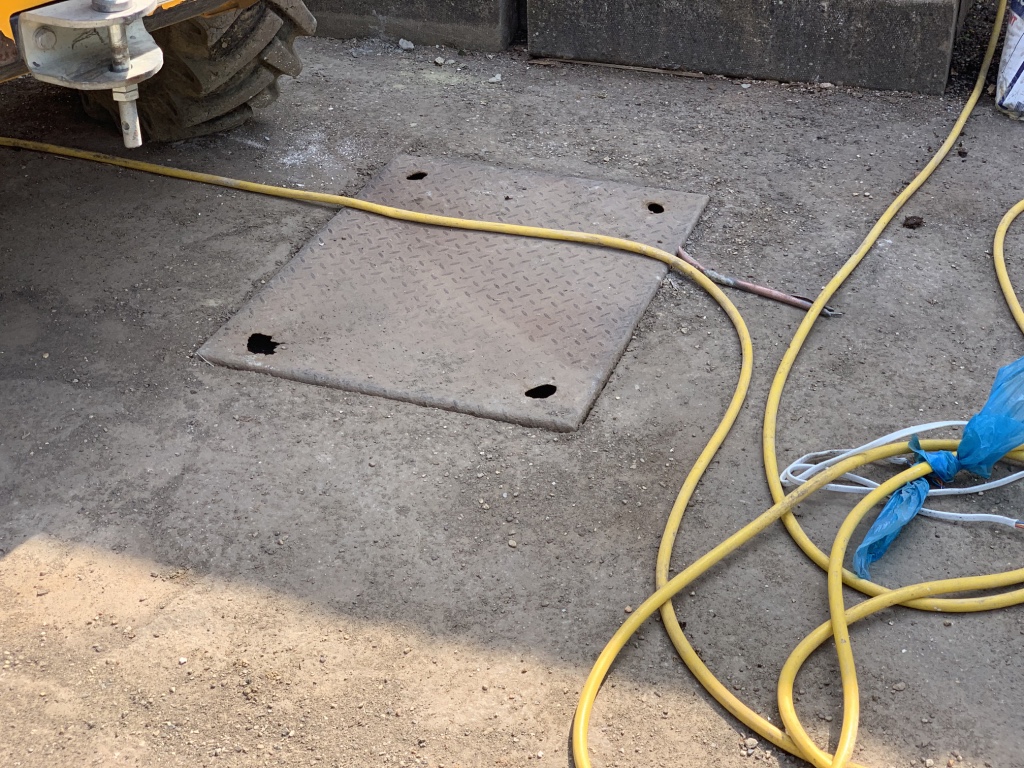
Inspection chamber rear of the property.
The inspection chamber at the rear of the building has an inspection lid covering with no seal.
The chamber is situated very close to the downpipe from the large roof. The downpipe from the roof points towards and is pouring only partially into a gully which gully has no surround. The roof water is flowing over the gully grid.
This gully discharges to a soakaway which we believe to be inadequate for its purpose.
We pumped approximately 700ltrs of clean water into the gully to test the soakaway and found the soakaway overflowed and flooded the immediate area within minutes. We continued to add water to demonstrate how the area is prone to flooding.
All inspection chambers and pipework to the rear of the building.
We found the pipes to and from the inspection chambers and gullies to have multiple defects throughout, allowing surface water from the flooded area, grass, and patio to soak through the ground and enter the sewage system via the open joints and displacements. We found the patio has subsided and is allowing water to pond.
In summary
The tests conducted show that there is an abundance of surface water entering the sewage system. Not only is this overwhelming the system, but this is also causing unnecessary wear and tear on the effluent pump, which pumps separated sewage water, as the pump is being overworked.
Advisement
We would like to refer you to our previous report dated 25th February 2019, which states the impact of surface water entering the foul system and our recommendation to carry out an inspection:-
We, therefore, propose the following:-
ESTIMATE
High-pressure Water Jetting and a CCTV drain inspection to confirm rainwater/surface water entering the foul system either directly or indirectly.
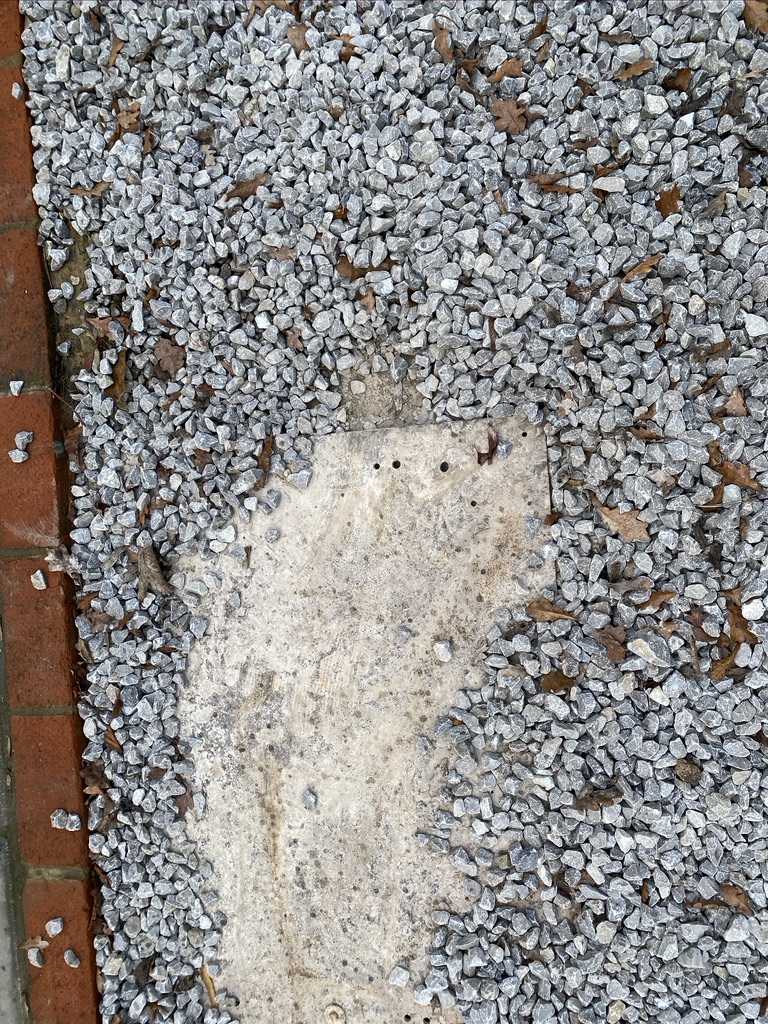
Our charge to carry out the above work is @£120.00 plus VAT per hour or part of, inclusive of labour and plant. We anticipate that we will complete this work in approximately 4 x hours.
RECOMMENDATION
Based on our observations, we propose the following:-
ESTIMATE
- To remove the steel plate and part of the path.
- To break out and remove the soft engineering bricks to the inspection chamber and the benching:
- To re-construct the inspection base and chamber to a standard conventional size, 600mm x 450mm concrete sections and torq strip.
- To supply and install a new double sealed inspection chamber cover and frame to suit.
- To supply and install approximately 14m of a resin-basted structural liner to effectively seal the pipework beneath the property as a means of repair.
The front of the property
The pipework right of the steel plate.
This run has an open joint, seems to be coated, and is also leaking. It needs to be cleaned and inspected, along with any other pipes at the rear of the property; confirm these pipes can be lined to save the removal of the footpath, including inspecting the lateral short pipe that runs under the building.
Once we have confirmed that these foul drainpipes can be lined our recommendation;
- Remove and replace the gully with a concrete surround.
- Structurally line the pipes up to the steel plate inspection chamber.
- Carry out a water test on the two inspection chambers with the sealed covers; if all is well, replace the broken rubber seal’s.
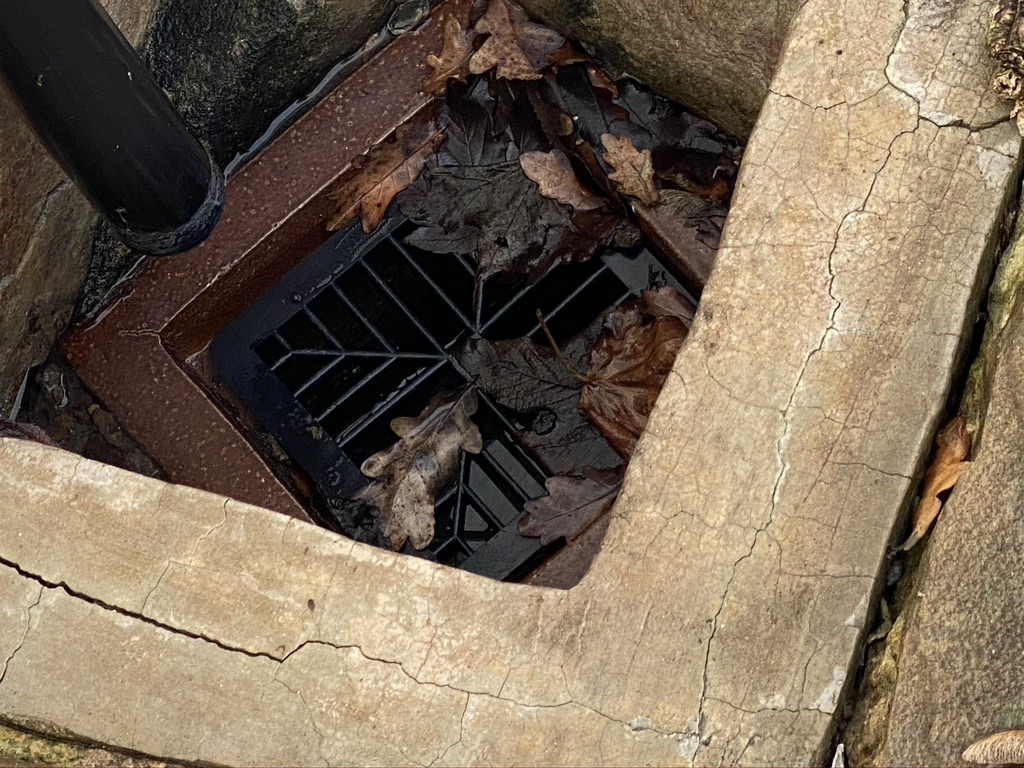
The rear of the property
- To break out and remove the defective/sunken gully and surround.
- To supply and install a new uPVC gully and surround it in concrete.
- To excavate from the gully to the inspection chamber located next to the garden wall pillar to the rear of the property, and connect using up to 5m of new 4” uPVC pipework.
- To surround the new pipe in shingle.
- To break out and reconstruct the inspection chamber located next to the garden wall pillar to the rear of the property.
- To supply and install a new double sealed inspection chamber cover and frame to suit.
- Replace the pipe from this inspection chamber next to the pillar up to the Inspection chamber before going under the building ???m (distance to be determined)
- To backfill excavated areas and leave flat. Any grass seeding, replacing of turf and finishing the patio to be carried out by others.
- To remove and dispose of excess spoil.
Our previous reports have brought to your attention the amount of fat found in the holding tank. I took a video recording as we emptied the tank as it was unbelievable. There was a 400mm thick layer of fat and lots of greases, a lot of which must’ve been forced through the holding tank into the treatment plant and the land drains.
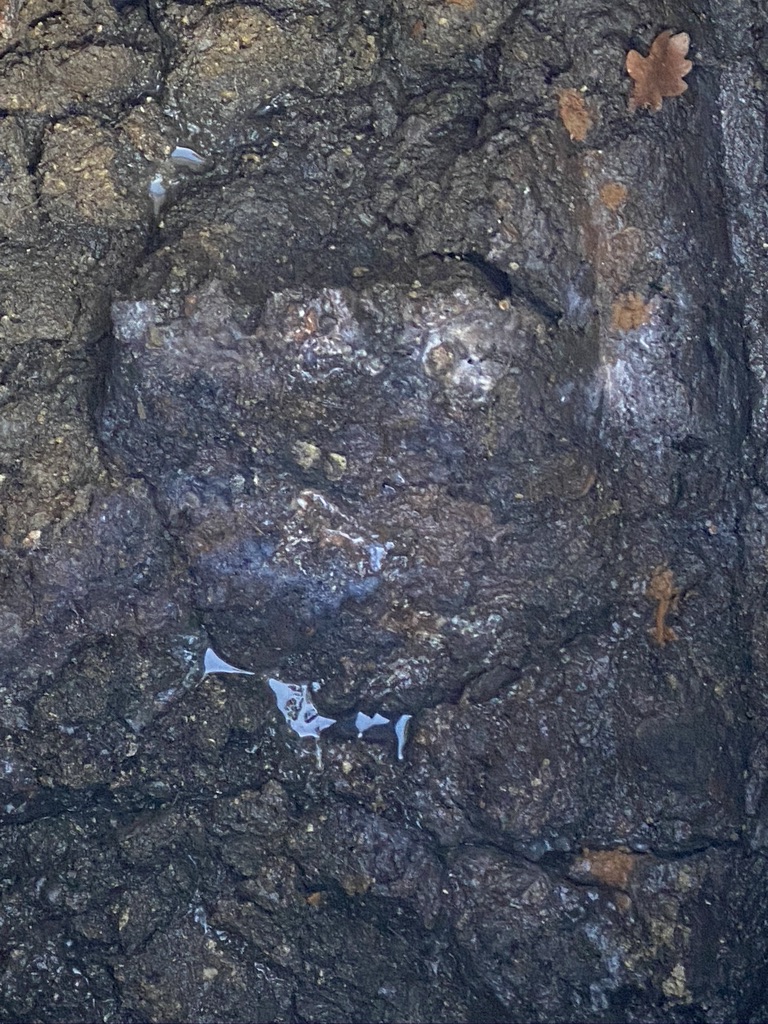
Our visual inspections of the chambers within the treatment plant often reveal grease and fats which have been pushed through into the second and the last chamber, covering the media.
This is seriously affecting the treatment process and allowing un-treated greasy water to flow into the land drains.
It would be best if you stopped allowing fat and grease into the sink leading to the holding tank of the treatment plant. Please confirm that you understand this?
The emptying of the holding tank revealed a large amount of fat and grease and highlighted the poorly fitted steel plate and large soakaway at the rear, which is not working; thus, the massive amount of water finding its way into the sewage system.
Furthermore, and I’m sure you can understand, we cannot reduce the recommended work by 45% or reduce the charges, and still achieve the quality of work required.
I urge you to read our reports detailing the amount of work required and why it is important and necessary to protect the treatment plant from surface water infiltration and especially fat and grease.
Our previous reports detail the work required on the sewage system around the house, and particularly the soakaway at the rear of the property for the large roof areas. As previously reported, this soakaway has been tested and is not working, as witnessed by yourself when we carried out the tests.
Furthermore, we have asked you for a copy of the invoice detailing the soakaway installation that is not working or at least put us in contact with the installer of the ill-fitted steel plate covering the inspection chamber to the front of the property. Also, you have not provided reasons why no double-sealed covers with rubber bands have been fitted to the inspection chambers at the rear of the property, where flooding regularly occurs, as confirmed by you in both our meetings.
I truly understand that it’s difficult to appreciate the impact of surface water on the foul treatment plant, which is why we have provided detailed reports, and many photos.
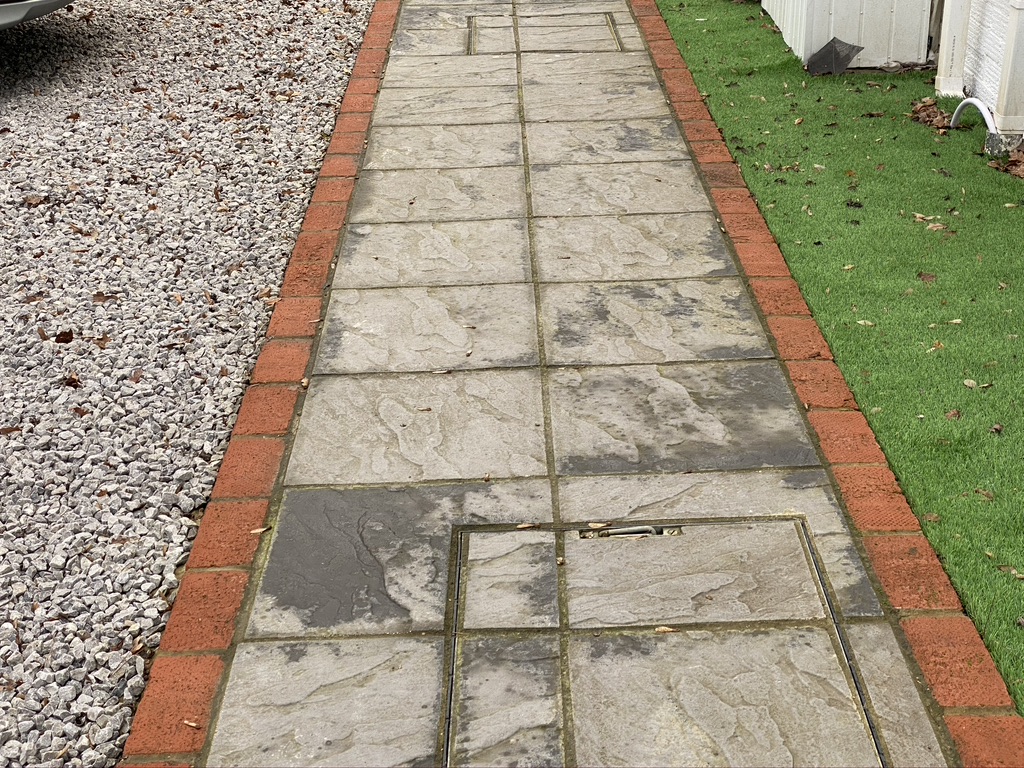
At the time of finishing the drive, which covered over the ill-fitted steel plate with gravel, and the installation of double-sealed covers at the front of the property, along with the work at the rear with the new installation of the soakaway for the surface water and roof water, and your electrician connected the treatment plant wiring to the gatepost, It appeared I had convinced you of my advice to avoid the infiltration of the surface water.
However, this was deemed not to be the case. I have included the following information to demonstrate that infiltration of surface water into a treatment plant is worth our attention. I include this in my letter to help explain the reasons for our concerns, which we hope will help:- [please see our blog article entitled ‘Rainwater is getting into your private sewage system’]
Conclusion
Customer’s duty and responsibility
The information must be given verbally and notices to be put up in a prominent position for the builder/ ground workers; to say 'warning', we have a private system and no rainwater connected to the sewage system.
Customers often say, “there is no rainwater in our system!” Customers also say, “we had a survey two years ago; there is no rainwater in our system!” “We haven’t got a problem; everything is working fine, everything goes away!”
Builders and building firms often use our company to install their customer's treatment plants, as we will see and pick up any issues during the initial survey. Builders often explain that their customers do not want a survey and will happily spend £20,000 on a new kitchen, but are reluctant to spend much on the drainage systems until it becomes an urgent situation.
When the problems start to be realized, customers are often in disbelief of how it could be the problem. Certainly, they do not believe that they are producing, or allowing, through the wrong connection of roof water to the sewage system, approximately 10,000 L - 20,000 L of additional volume into the foul system during a period of 24 hours of medium rainfall.
To demonstrate, these white containers hold 1000 L. After connecting a rainwater downpipe from a large roof, each of these containers will take less than an hour to fill up during medium rainfall.
Please note that you do not meet the binding rules if you have surface water entering the system directly or indirectly.
You’re an operator if any of the following is true:
- You own the property that uses the system.
- You own a property that shares the system with other properties - each property owner is an operator, and you’re jointly responsible for complying with the general binding rules.
- You have a written agreement with the property owner that says you’re responsible for the system’s maintenance; for example, you’re renting, and it’s in your tenancy agreement.
If you are ‘The operator’ of a septic tank or small sewage treatment plant, you will not need a permit if you meet all of the general binding rules that apply to you.
If you allow rainwater to drain into the public sewer, especially a treatment plant, you’re in breach of the binding rules. Imagine during a heavy downpour, allowing the surge of rainwater to disturb the separation taking place in the initial first chambers of the public treatment works.
Direct Connections from roofs, surface water pipes connected to the sewerage system. The effect of 1000 houses of the combined roof or surface water in the public sewerage system is unbelievable. Causing an overuse in some cases, 24,000 L per 24 hours to public treatment works from each property.
Roof and surface water
Site investigations must be undertaken thoroughly and competently so that all aspects of soil properties, geo-technology and hydrogeology are adequately reviewed alongside the hydraulic design of soakaways.
SURFACE WATER WARNING
Please note that ASL Ltd is not liable for any surface water entering the system; therefore, any estimate excludes provisions for surface water that may or may not be entering the foul water system. If surface water/rainwater can enter the tank, this can cause further problems with separation/treatment. If the water enters in a surge, such as during heavy rainfall, or a storm, the incoming water can stir up the first tank, destroying any separation that has occurred in the primary settlement chamber and or any treatment. Without adequate separation, suspended solids and fats can pass through the tank and on through to the soakaways/drainage field, where they can coat the surface, causing irreparable damage making it progressively waterproof. This diminishes the soakaway’s / drainage fields' ability to dissipate water until it ceases to work altogether.