Case Study | What is the right size of a Treatment Plant?
When installing a private sewage treatment plant, discussions about the right solution for you are so important. To trust is imperative.
As drainage specialists, our aims are to:
- Save time.
- Achieve quality.
- Be cost-effective. AND
- Protect our land, rivers, and streams.
The following case study will help explain the importance of accurate disclosure of information in the planning process.
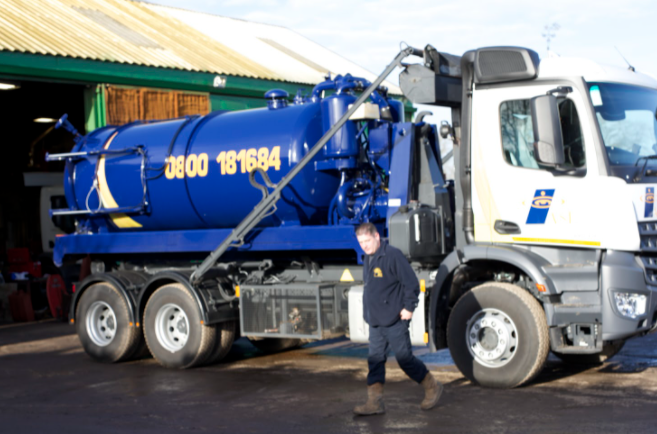
At a recent meeting with the owner of the property in question – I observed that when calculating the size of the treatment plant required – talking about reference numbers for the model of a treatment plant, doesn’t relate to what is being taken away to the public treatment works and is therefore difficult for the customer to quantify;
I put this to the estate manager, who became very annoyed and agitated.
I had explained to him at the last meeting that “we need our credibility, and we need to trust each other to give the correct information otherwise the whole exercise is futile, incapable of producing any useful result, expensive, and disruptive.”
The contents of a treatment plant i.e. a heavy density of solids over a short period indicate a higher number of people using the system, possibly a very high flow rate.
When there is double the flow, entering the tank in a surge, such as at the busiest time, (especially if the space needed to separate in the holding tank has been jeopardized) the incoming sewage and water can stir up separation settlement that has occurred in the first tank, bypass the primary settlement chamber and flow through the system untreated.
The suspended solids, unwelcome fats, and especially oil, or grease substances can pass through the tank, and on through into the land drainage causing pollution to the drainage field. These unwelcome pollutants can coat the surface, causing irreparable damage, making it progressively and waterproof. This diminishes the ability of the drainage field to dissipate the now contaminated dirty greasy water from the struggling treatment plant until both the plant and the land drains cease to work altogether.
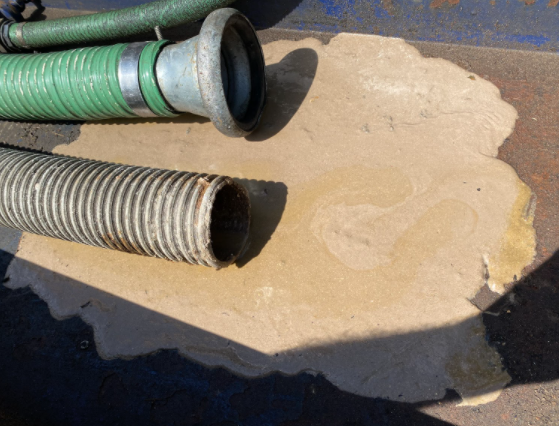
Observations & Findings
The property in question is a new build.
On the first emptying approximately six weeks after occupancy of the tenants, our under manager, Fred, and the tanker driver, who is very familiar with treatment plants, attended with the tanker, in response to a request from the tenants.
After removing the large lid off the treatment plant he found that the holding tank was overfilled with excreta, unwelcome thick fat, oil, and lots of grease. He commented that there were lots of people coming and going.
At the time of the inspection, it was found that the treatment plant was struggling to work. The bacteria covered the whole of the wheel, (indicating maximum capacity) the electric motor was having difficulty powering the big wheel (in only six weeks since the occupants moved in).
Based on my experience, the excreta, fat, grease, and oil inside the tank indicated numbers of around 40 people plus, using the system (over this short period). Three times the recommended use for the system.
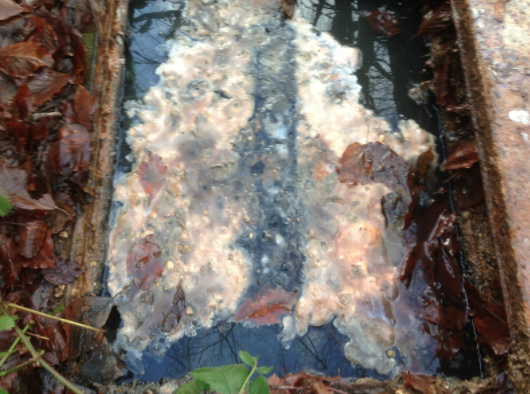
During my visit, I was explaining the situation to a gentleman who seemed to be overseeing what I was doing, who volunteered the information that there were lots of people on site. As we were talking, the operation manager of the estate interrupted and denied that there were a lot of people, ten minutes later he approached me and said that he may have forgotten to mention there had been many construction contractors on site for the last six week period, but they had now left and the numbers would now be much lower i.e. around eight or ten people, certainly no more.
He also continually repeated to me that I was mistaken about the fat, oil, and grease, as they did not use fat and firmly stated no oil was going down the sink.
I arranged with the operations manager that we empty the system again in six weeks and check how it was functioning. Based on the operation manager informing us that the contractors had left and the numbers were now low, I reminded him again that I could not calculate anything unless I knew the exact numbers.
Before the six weeks agreed emptying period came about we received an emergency call.
One of our blocked drain engineers attended the estate to investigate ‘water bubbling out of the ground in the upper field’. On arrival, he found smelly untreated treated water bubbling out of the ground. The land drains had ceased to function.
He reported that there were a lot of people around, and lots of activity to and from a very large kitchen and sitting area, a newly installed kitchen in storage and garage wooden building, seven meters from the treatment plant, which was smelling profusely.
He found that the treatment plant was completely overwhelmed. He contacted the office to redirect a tanker to carry out an emergency emptying.
There was a solution to this situation. Even though the damage had already been caused, due to using the system without a grease trap for a 6 to 8 week period; seemingly unaware of unhealthy behaviors in the kitchen; no conversations to create a healthy environment within the treatment plant for bacteria to thrive; and no awareness or attempt to reduce risk when large events and gatherings are held.
Once the treatment plant has been completely overhauled and repaired and the land drains completely replaced, we realize how important it is to have such meetings at the start of the process, saving time and reducing costs.
I shared with him that many of my other customers are proactive, and discuss the situation, which allows options. In this case, the treatment plant, we could have increased the holding tank by installing a temporary 1000 gallon tank before the treatment plant or emptying the tank more frequently. I would need approximate average numbers of meals; personal using the kitchen, so that we could then install an appropriate industrial type grease trap.
During this emergency emptying of the treatment plant on this occasion, we found:
- The gearbox was not working, and the treatment plant was overwhelmed with solids, grease, oil, and fat.
- The excreta contents inside the tank indicated 35 personnel plus, using the system
- The motor was found to be completely burnt out.
- The new combined motor and gearbox had only been used for 12 weeks in total. (Bear in mind that this was an enclosed standard motor, lubricated with grease and a grease-filled gearbox, neither of which require any maintenance during the running of the unit
- under normal operating conditions)
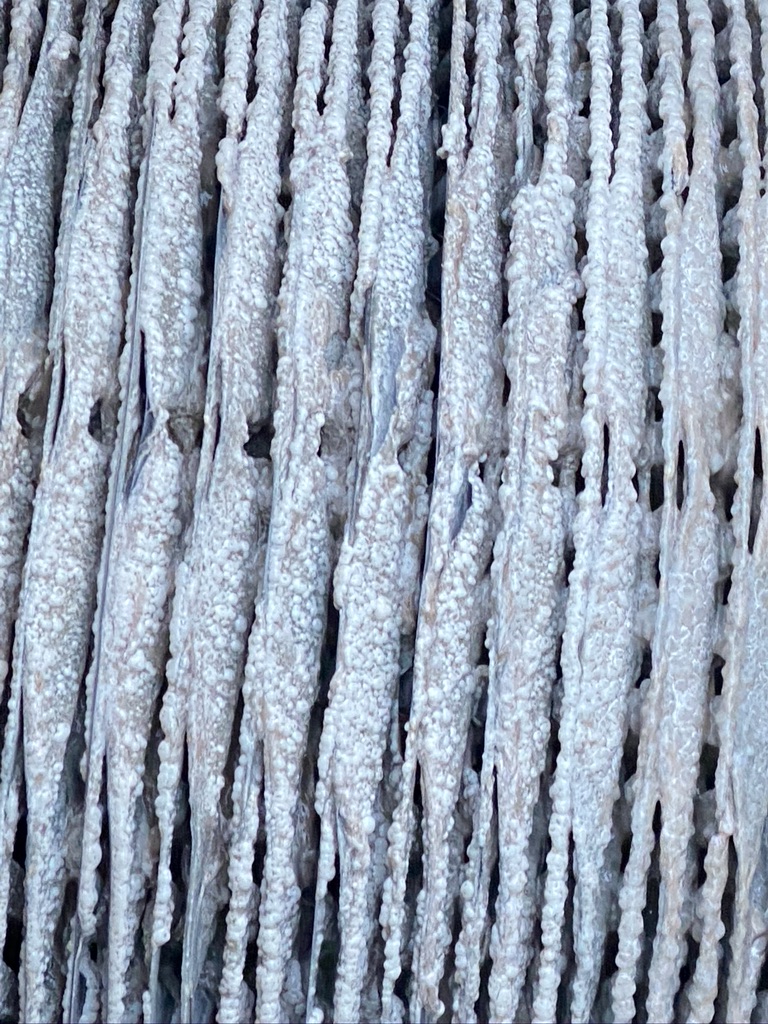
As a result of fat covering the wheel, the strain had at least damaged, possibly burnt out, the electric motor powering the combined gearbox. There was far too much radial force applied to the gearbox output shaft, which was, in turn, having difficulty turning the big wheel.
The manufacturer refused to replace the motor under the guarantee due to the result of overuse, fat oil, and grease.
To pursue and defend the situation, would be futile and go on for far too many months.
There was a lot of pressure, as we were having to empty the tank every two days, you can imagine the disruption and the cost.
To produce clean water in the shortest amount of time, I ordered a replacement motor and gearbox, and fitted a new belt, at ASL’s expense.
It’s my understanding that the operations manager purchased the wrong type, installing two or three very small grease traps in the kitchen. Approximately two weeks after my first visit. Grease, oil, and fat were still evident in the holding tank 12 weeks after the first emptying, which is understandable as the very small grease traps were too small, not purchased or installed inside the kitchen until 2 to 3 weeks after my last visit.
I was disappointed that there was no discussion regarding the type of grease trap and the size, before purchase. When ordering a grease trap you need to give numbers of personnel using the system, to enable our company to calculate which fat and grease trap is appropriate.
I believe that most of the damage to the land drains occurred during the first eight weeks, including the damaged burnt-out motor. I was concerned that the treatment plant was far too close to the seating area and the kitchen area. This was very apparent on both visits exacerbated as the treatment plant was overwhelmed and smelling, contaminating both areas.
Our original calculation was based on eight bedrooms plus a one-bedroom flat and one additional toilet in the storage and garage area.
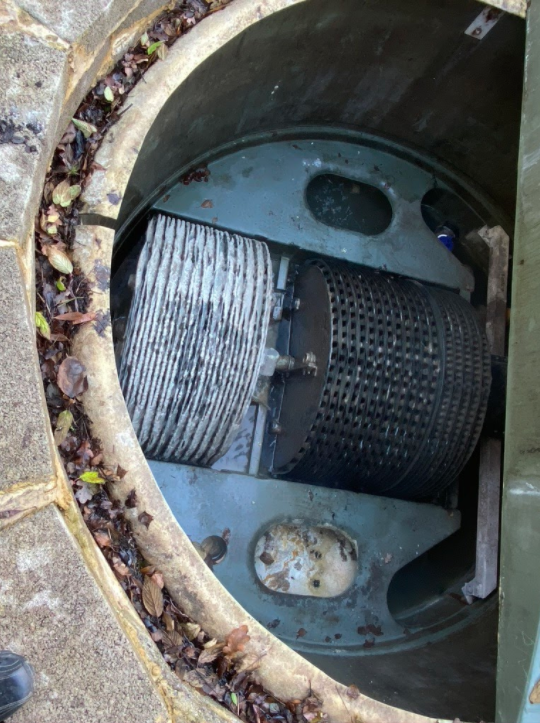
There had been no meeting, no discussion or plan before the kitchen installation, or the positioning of the seating area next to the treatment plant.
No allowances have been made for what seems to be similar to a commercial training facility, or an outdoor skills centre with overnight accommodation for visitors.
Questions I have been asking.
The current list of properties connected to the system (see below), are these permanent residential properties, or are these accommodation for guests staying over for two or three days or a week?
- A residential rather than domestic, calculation, these alone would exceed 3,500 litres per day.
- Estimated 150 litres per day to 200 litres per day, per person.
- 8 bedroomed large country house 14 persons
- 1 large flat
- 8 mobile caravans with mains water - 16 persons (two persons per caravan) with a separate kitchen and canteen capable of serving 15 to 20 people at least.
On the times I have visited, the flow from the kitchen has been constant, as has been the flow from the main house.
Whether the high numbers only last for seven days, depending on occupancy, at a time when the holding tank is overfull, this is sufficient to overwhelm the treatment plant and land drains, causing considerable damage.
Testing the drains looking for rainwater roof water in the system
During the testing of the drains under ideal conditions i.e. no rainfall for more than 14 days, The operations manager and Chris made sure that there was no flow of water from the kitchens, or the house or the caravans, it was ascertained that there was no surface water entering the treatment plant via the drains indirectly or directly
The existing treatment plant without a commercial grease trap is simply too small for the above numbers.
Conclusion
The seating area and the kitchen where hot food is served – My understanding:
Under building regulations Part H section 2.21, it specifies that ‘kitchens, commercial hot food premises to be fitted with a grease separator complying with the rules and designed following effective means of grease removal’ before the kitchen starts to operate or discharge.
By using a grease trap calculator we can influence and recommend suitable grease management systems. We need numbers for the calculation. We can then determine the correct size.
I am particularly worried about how close the kitchen and the seating area is to the treatment plant. we need to check it complies with the necessary regulations, at least we should consider a risk assessment.
The exact calculation regarding the treatment plant would be carried out after receiving the true figures. When installing a treatment plant, to avoid misgivings: two people per bedroom. The main house has eight bedrooms, therefore we have to allow for a potential 16 people plus allow for expansions: large events and gatherings.
We calculate on “potential”, or written instructions from the tenant or client, i.e., the tenants would give us numbers of guests, plus expected visits, with or without an overnight stay. All this information would be given before using the house. The kitchen would only be installed, and the seating area decided during a planned meeting to discuss the use of the area, and the quantities involved. Grease traps would be installed before using the kitchen.